Our Process
Why Powder Coating?
Powder coating produces a durable coating which is tough, hard, and abrasion resistant and the choice of colors and finishes are limitless. Environmentally friendly, the application emits nearly zero volatile organic compounds (VOC's).
The Powder Coating Process...
Step 1. Preparation of the surface at MPC starts with a process to insure that the surface is properly cleaned and free of "soils" such as manufacturing oils. Subsequent surface treatments might include blasting, and iron phosphate or zinc phosphate depending on the long term corrosion performance desired. Special high temperature masking can be applied to most surfaces such as threading or tolerance areas to avoid coating.
Step 2. Application of the powder and MPC uses Thermoset powders. The particles of powder are given an electrical charge in the powder coating gun. The targeted part is attached to a rack that is grounded. The electrically charged powder particles are attracted to the grounded part and attach themselves like little magnets to the part. The particles build-up on the surface of the part until it is covered with charged particles and the part surface is charged. At this point the oncoming particles are actually repelled by the charged particles on the part and the coating process stops. Since the powder is applied dry, there is no worry of drips as there is with traditional wet-painting methods.This provides an even film thickness.
Step 3. Heating and Curing. The surface and the powder are then heated and as the temperature rises past the melt temperature of the powder, it will melt and to the surface. The temperature is maintained while the coating material cures and forms a strong, hard, continuous film.
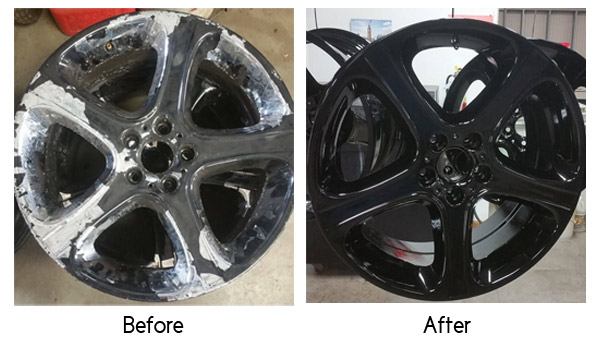
Why Powder Coating?
Powder coating produces a durable coating which is tough, hard, and abrasion resistant and the choice of colors and finishes are limitless. Environmentally friendly, the application emits nearly zero volatile organic compounds (VOC's).
The Powder Coating Process...
Step 1. Preparation of the surface at MPC starts with a process to insure that the surface is properly cleaned and free of "soils" such as manufacturing oils. Subsequent surface treatments might include blasting, and iron phosphate or zinc phosphate depending on the long term corrosion performance desired. Special high temperature masking can be applied to most surfaces such as threading or tolerance areas to avoid coating.
Step 2. Application of the powder and MPC uses Thermoset powders. The particles of powder are given an electrical charge in the powder coating gun. The targeted part is attached to a rack that is grounded. The electrically charged powder particles are attracted to the grounded part and attach themselves like little magnets to the part. The particles build-up on the surface of the part until it is covered with charged particles and the part surface is charged. At this point the oncoming particles are actually repelled by the charged particles on the part and the coating process stops. Since the powder is applied dry, there is no worry of drips as there is with traditional wet-painting methods.This provides an even film thickness.
Step 3. Heating and Curing. The surface and the powder are then heated and as the temperature rises past the melt temperature of the powder, it will melt and to the surface. The temperature is maintained while the coating material cures and forms a strong, hard, continuous film.